Laser Cutting UK
Custom Gaskets for Every Application
Stephens Gaskets is Your Reliable Supplier for Laser Cutting
Call 0121 544 5808 Today
Bespoke Manufacturing
Instant Quote Service
Worldwide Delivery
Various Gauges/Thicknesses
Bespoke Manufacturing
Instant Quote Service
Worldwide Delivery
Various Gauges/Thicknesses
Laser Cutting UK – Precision Engineering by Stephens Gaskets
When it comes to precision engineering, laser cutting is at the forefront of modern manufacturing, offering unparalleled accuracy and versatility. Stephens Gaskets, a leader in this field, is proud to offer top-tier laser cutting services across the UK, Europe, and to customers around the world. Whether you’re working on a complex industrial project or a small custom order, our state-of-the-art laser cutting capabilities ensure your specifications are met with precision and quality.
Why Choose Stephens Gaskets for Laser Cutting in the UK?
At Stephens Gaskets, we understand that every project is unique, requiring a tailored approach to meet your specific needs. Our laser cutting services are designed to offer you the highest level of accuracy, efficiency, and reliability, ensuring your projects are completed to the exact standards you require.
Expertise and Experience
With decades of experience in precision engineering, we’ve honed our laser cutting techniques to provide exceptional results for a variety of materials and applications. From automotive to aerospace, electronics to industrial machinery, our expertise spans a wide range of sectors, making us a trusted partner for businesses across the globe.
Cutting-Edge Technology
We invest in the latest laser cutting technology to ensure that every project is executed with the utmost precision. Our advanced machinery allows us to cut a wide range of materials, including metals, plastics, and composites, with exacting accuracy. Whether you need intricate designs or large-scale production, our equipment is up to the task.
Commitment to Quality
Quality is at the heart of everything we do. Our rigorous quality control processes ensure that every piece we produce meets the highest standards of excellence. We understand that even the smallest imperfection can have significant consequences, which is why we take great care in every step of the laser cutting process.
Global Reach with a Local Focus
While we are based in the UK, our services extend far beyond our borders. We serve customers across Europe and around the world, delivering the same high standards of precision and quality regardless of location. Our global reach is a testament to our ability to meet the diverse needs of our clients, no matter where they are.
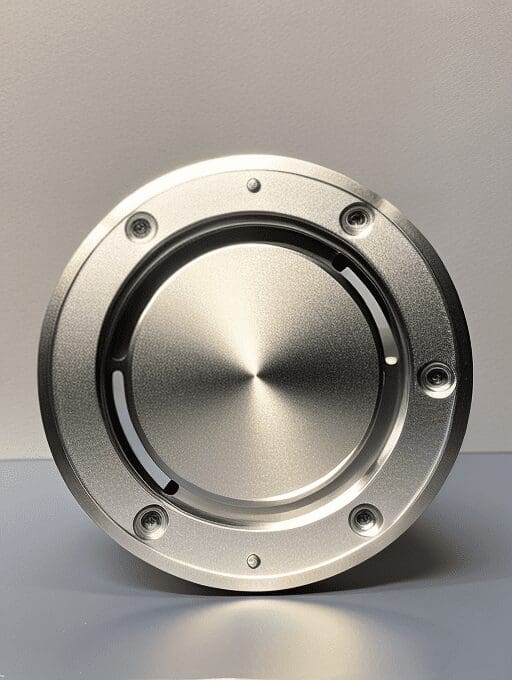
What is Laser Cutting and Why is it Important?
Laser cutting is a precise and efficient method of cutting materials using a high-powered laser beam. This technology allows for the creation of intricate designs and detailed cuts that would be difficult or impossible to achieve with traditional cutting methods.
Precision & Accuracy:
Laser cutting provides unparalleled accuracy, ensuring that even the most complex designs are executed with precision.
Versatility:
Laser cutting can be used on a wide range of materials, including metals, plastics, and composites.
Efficiency:
Laser cutting is a fast and efficient process, reducing lead times and increasing productivity.
Minimal Waste:
The precision of laser cutting minimises material waste, making it an environmentally friendly option.
Our Laser Cutting Services: Meeting Your Specific Needs
At Stephens Gaskets, we offer a comprehensive range of laser cutting services tailored to meet the unique requirements of our clients. Whether you need custom parts for a one-off project or high-volume production runs, we have the capabilities to deliver exceptional results.
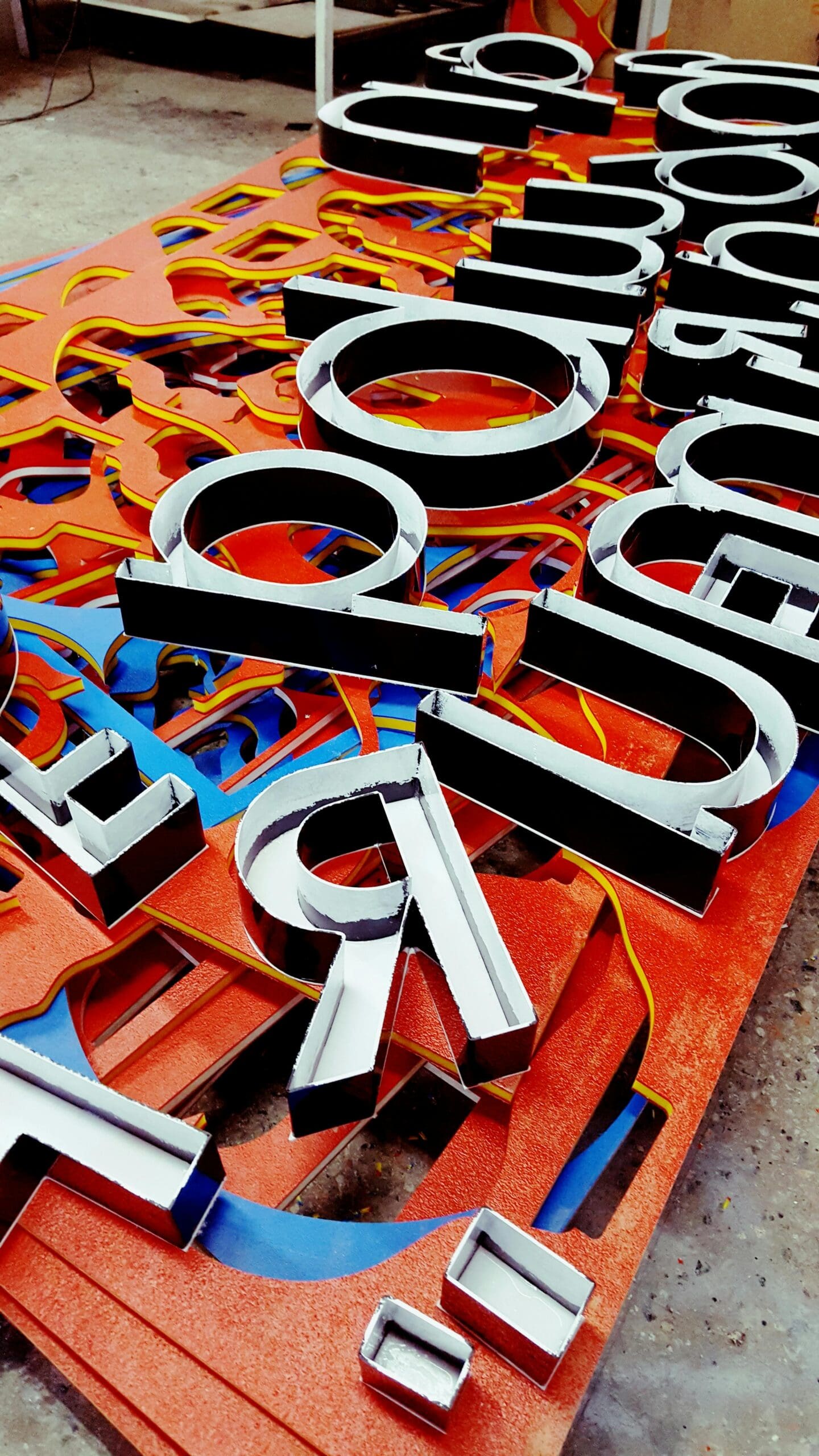
Custom Laser Cutting
No two projects are alike, and we understand the importance of delivering customised solutions that meet your exact specifications. Our team of experts will work closely with you to understand your needs and develop a laser cutting solution that aligns with your project goals.
High-Volume Production
For clients who require large quantities of precision-cut parts, our high-volume production services are the ideal solution. We have the capacity to handle large orders efficiently without compromising on quality, ensuring that you receive your parts on time and to the exact specifications.
Material Capabilities
Our laser cutting services are not limited to a single material. We work with a wide range of materials, including:
- Metals: Stainless steel, aluminium, copper, and more.
- Plastics: Acrylic, polycarbonate, and other engineering plastics.
- Composites: Carbon fibre, fibreglass, and more.
Each material presents its own challenges, and our team has the expertise to deliver precise cuts regardless of the material.
The Future of Laser Cutting: Embracing Innovation at Stephens Gaskets
As technology continues to evolve, so too does the field of laser cutting. At Stephens Gaskets, we are committed to staying at the forefront of these advancements, ensuring that our clients benefit from the latest innovations in precision engineering.
Integrating New Technologies
We are constantly exploring new technologies and techniques to enhance our laser cutting services. Whether it’s through the adoption of more efficient laser systems or the integration of AI-driven processes, we are always looking for ways to improve our services and deliver even greater value to our clients.
Sustainability and Environmental Responsibility
As part of our commitment to sustainability, we are continually refining our processes to minimise waste and reduce our environmental impact. Laser cutting is inherently a low-waste process, but we are dedicated to finding new ways to make it even more environmentally friendly.
Expanding Our Global Reach
Our goal is to continue expanding our services to new markets around the world. By building strong relationships with clients across Europe and beyond, we are positioning ourselves as a global leader in precision laser cutting.
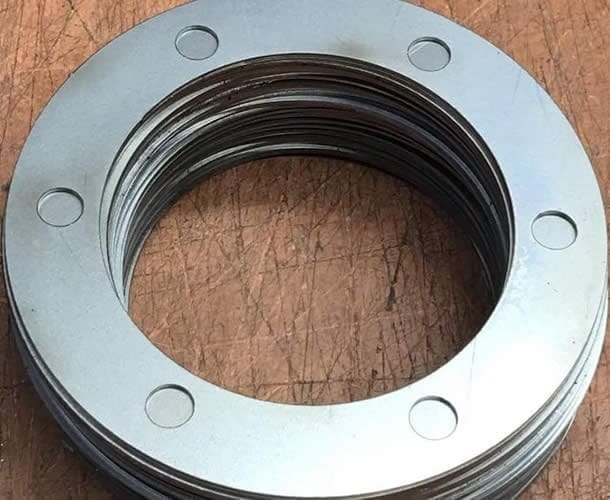
Partnering with Stephens Gaskets: Your Gateway to Precision
When you choose Stephens Gaskets for your laser cutting needs, you’re choosing a partner dedicated to delivering excellence. Our commitment to quality, innovation, and customer satisfaction sets us apart in the industry, making us the preferred choice for businesses across the UK and around the world.
Ready to take your project to the next level? Contact Us today to learn more about our laser cutting services and how we can help you achieve your goals.
FAQs
What materials can Stephens Gaskets cut using laser technology?
We can cut a wide range of materials, including metals, plastics, and composites. Our advanced machinery allows us to handle materials of various thicknesses and densities, providing precision cuts every time.
How accurate is laser cutting compared to other cutting methods?
Laser cutting offers unparalleled accuracy, with tolerances as tight as ±0.1mm. This level of precision is difficult to achieve with traditional cutting methods, making laser cutting the preferred choice for projects that require intricate designs and exact specifications.
Is laser cutting cost-effective for large production runs?
Yes, laser cutting is highly efficient and can be very cost-effective for large production runs. The speed and precision of laser cutting reduce the overall production time, which can lead to significant cost savings, especially for high-volume orders.
Can Stephens Gaskets handle custom designs?
Absolutely. We specialise in custom laser cutting and can work with you to bring your unique designs to life. Whether you need a single prototype or a large production run, we have the capabilities to meet your needs.
Do you offer laser cutting services outside of the UK?
Yes, while we are based in the UK, we serve clients across Europe and around the world. Our global reach allows us to deliver high-quality laser cutting services to clients no matter where they are located.
Need Guidance on Laser Cutting?
Stephens Gaskets is a leading supplier of high-quality Laser Cutting. With over 70 years of experience in the industry, we have a deep understanding of the needs of our customers. We commit ourselves to providing top-notch products and services for companies nation wide.
Get in touch with us today to learn more about our Laser Cutting and how we can help you with your next project.