Flange Gaskets

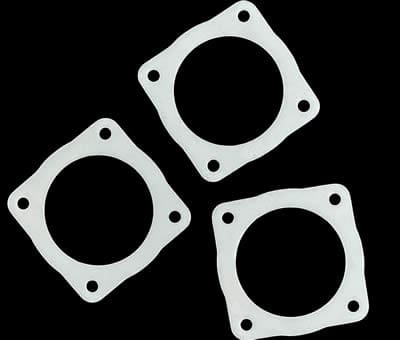
Flange Gaskets for Leak-Free Sealing in Pipes and Equipment
Call 0121 544 5808 Today
Bespoke Manufacturing
Instant Quote Service
Worldwide Delivery
Various Gauges/Thicknesses
Bespoke Manufacturing
Instant Quote Service
Worldwide Delivery
Various Gauges/Thicknesses
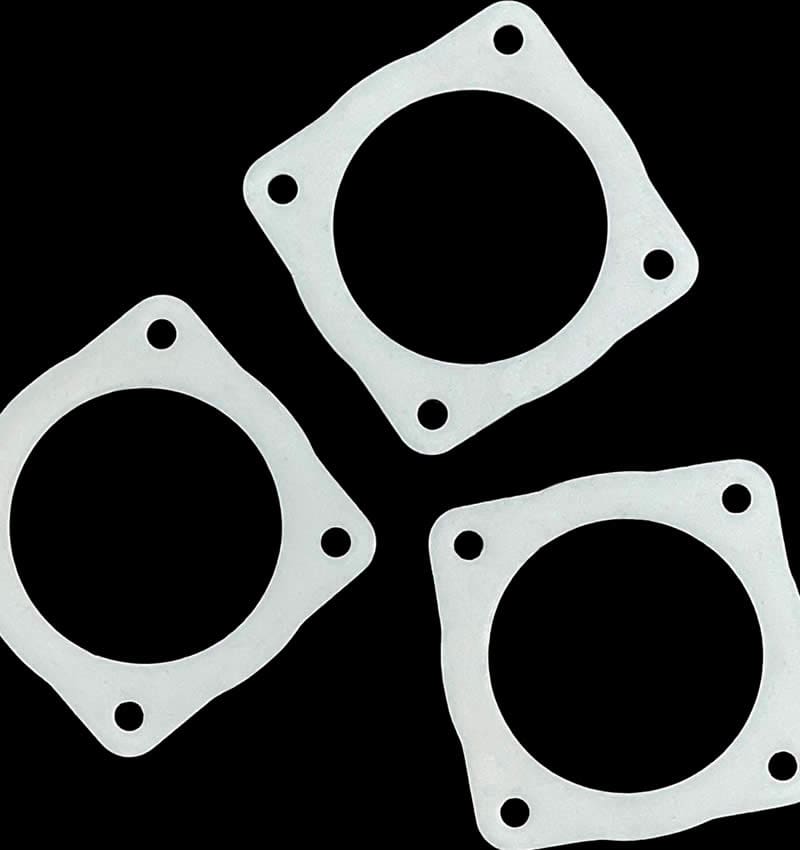
What Is a Flange Gasket?
A flange gasket is a precision sealing element placed between two flanges to create a leak-proof joint when the flanges are bolted together. It compensates for surface imperfections and fills gaps that could otherwise allow fluids or gases to escape.
Flange gaskets are essential in systems carrying liquids, vapours, or gases under pressure. They are available in various styles – such as ring gaskets (sealing only the flange face) and full-face gaskets (covering bolt holes as well).
The choice of gasket material depends on factors like:
- Temperature range.
- Pressure rating.
- Type of media (water, steam, oil, gas, chemicals).
- Flange surface finish and bolt load.
Benefits of Flange Gaskets
1. Leak Prevention
Flange gaskets form a reliable seal under compression, helping prevent costly leaks that compromise safety, productivity, and environmental compliance.
2. Compensation for Surface Irregularities
Gaskets fill the fine grooves, scratches, or machining marks that exist on even new flange faces, ensuring a uniform seal.
3. Resistance to Pressure and Temperature
By choosing the right material, flange gaskets can withstand high temperatures, pressure surges, and fluctuating thermal conditions.
4. Vibration and Shock Absorption
Flexible gasket materials help dampen vibration or thermal expansion, reducing the risk of bolt loosening or fatigue over time.
5. Corrosion Barrier
Certain gaskets isolate metal surfaces from one another, helping prevent galvanic or chemical corrosion in corrosive environments.
6. Easy Installation and Maintenance
Most flange gaskets are easy to install and replace, minimising maintenance time and ensuring long-term reliability.
7. Cost Efficiency
Flange gaskets reduce the likelihood of leaks, system failures, or shutdowns, saving time and money on both emergency repairs and production losses.
Applications of Flange Gaskets
Flange gaskets are used in any system where two flanged surfaces are joined and must be sealed under pressure. Typical industries and use cases include:
Common Flange Gasket Materials in Manufacturing
Selecting the right gasket material depends on the media being handled, system pressure, temperature, and regulatory requirements.
1. Rubber (NBR, EPDM, Neoprene, FKM)
Used for general water, air, and low-pressure oil sealing. Cost-effective and easy to handle.
2. PTFE (Teflon)
Inert and hygienic, ideal for chemical and pharmaceutical systems. Resists acids, solvents, and high temperatures.
3. Graphite
Used for steam, hot oils, and high-temperature, high-pressure environments. Maintains sealing integrity under thermal cycling.
4. Compressed Non-Asbestos Fibre (CNAF)
Suitable for oils, water, steam, and mild chemicals. Versatile and asbestos-free.
5. Metallic and Semi-Metallic Gaskets
Spiral wound, ring-type joints, and kammprofile gaskets are used for extreme pressures and thermal conditions.
6. Fibre (Cellulose, Aramid)
Used in lower-pressure applications. Easy to cut and install; ideal for pump and valve gaskets or older equipment.
Our team can guide you through chemical compatibility, flange pressure classes, and installation best practices.
Common issues solved by Flange Gaskets
Flange Gaskets prevent many costly and dangerous system failures. When correctly selected and installed, they solve several recurring problems in industrial systems:
- Incorrect Material Selection
Using the wrong material can cause chemical degradation or thermal breakdown. Always match gasket composition to media and operating conditions. - Installation Errors
Over- or under-tightening bolts can cause gasket damage. Flange faces must be properly cleaned and aligned. - Compatibility with Flange Type
Different flange types require specific gasket styles. For example, metal gaskets are only suitable for high-quality, smooth flange finishes. - Gasket Creep and Relaxation
Heat and pressure can cause some gasket materials to relax over time. This can be mitigated with high-performance materials like graphite or reinforced composites. - Stocking Challenges
Having too many sizes and materials in stock increases overhead. A versatile gasket programme simplifies inventory and ensures readiness. - Maintenance Downtime
Choosing higher-quality gaskets may increase service life and reduce the need for frequent changeouts or unplanned shutdowns.
Why Choose Stephens Gaskets?
As a UK Flange Gaskets manufacturer, Stephens Gaskets provides expert solutions for industrial, marine, utility, and engineering customers.
Our customers trust us for:
- High-quality materials including PTFE, graphite, rubber, CNAF, and spiral wound.
- Accurate cutting and custom sizing.
- Fast delivery of both standard and non-standard formats.
- Technical support for media compatibility and system performance.
- Cost-effective supply for production, repair, and maintenance.
Contact Stephens Gaskets
We supply Flange Gaskets you can rely on – built to last and ready to seal.
Looking for dependable flange gaskets with quick delivery and expert support?
Contact us today for a quote, technical advice, or custom sizes.